Sustainability
TRICOYA
LOOKING TO THE FUTURE
All wood used in the Tricoya® production process is sourced from sustainable resources such as certified, reclaimed or recycled timber.
CREDENTIALS
Tricoya is EUTR compliant and is produced from fast-growing, well managed, legal sources.
With superior durability and stability Tricoya has a considerably longer lifespan than unmodified wood products which leads to lower maintenance frequency.
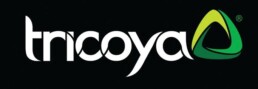
Sustainability Brochures
The Product
TRICOYA Sheet and Processing
The Product
Tricoya® can be cut, coated, sanded, glued, machined and fastened the same as any other high performing wood fiberboard – allowing users all the freedom associated with MDF. The Tricoya® difference is that this can now be done for the outside and with confidence.
THICKNESS | STOCK SIZE | SPECIAL ORDER |
---|---|---|
6mm | 1220×2440 | N/A |
9mm | 1220×2440 | 3050 |
12mm | 1220×2440 | 3050 |
15mm | 1220×2440 | 3050 |
18mm | 1220×2440 | 3050 |
Other sizes may be produced upon request and typically associated with a minimum order quantity. Custom thicknesses between 5mm, and 18mm, can be produced for quantities of at least one container.
PROCESSING Tricoya®
To ensure you get the best performance possible from Tricoya®, and the coatings and fixings you will use with Tricoya®, it is important that you adhere to the following guidelines;
Tricoya® may be cut and machined in the same way as other wood fibreboards with no change in machinability. Tricoya® is delivered with a 120 grit sanded finish. It may be sanded with finer papers to achieve smoother surfaces. Water and solvent based paint systems may be used to decorate Tricoya®. Tricoya® may be laminated with melamine papers, high pressure laminates, wood veneers, foils and other materials. Exterior adhesives such as epoxy, polyurethane, phenol-resorcinol resin and EPI may be used as long as they meet exterior use requirements.
If you are coating or painting on Tricoya® you must use a primer coat (first coat) that is extremely low or is free of calcium carbonate.
All faces, sides, edges and cuts must be totally sealed with this primer.
All edges must be machined eased to ensure edges are fully sealed.
Coatings and paints must contain an anti-fungal additive.
Any cuts made after coating or painting need to be sealed with the above primer.
All subsequent paint coats can contain calcium carbonate.
Any fasteners and fixings that are fixed into the Tricoya® panel need to be Stainless Steel 304.
Any fasteners and fixings that are in direct contact with the bare Tricoya® panel need to be Stainless Steel 304.
Any seashore application will require any fasteners and fixings to be Stainless Steel 316.
When Tricoya® is fully painted, coated or overlaid, coated hardware such as epoxy, lacquer, PU or powder coated can be used for applications in DRY locations (where moisture does not build up) or where the condensation exposure is low.
The Residual Acetic Acid in Tricoya® is less than Accoya® however, this does not mean you can use non corrosion proof metals directly with Tricoya®.
Other metals – Galvanised metals or zinc alloys are not corrosion-proof when used with Tricoya® or Accoya®. The surface of certain aluminium alloys, copper, lead and other metals may also oxidise. Experience to date on the use of solid brass has been positive, especially on brass that is factory clear coated to retain brightness. Chrome plated steel performed very well in testing but if the protective layer is damaged this product will be susceptible to local accelerated corrosion.
The Product Brochures
Applications
Unlimited uses
Applications
The market for Tricoya wood based composites includes, but is by no means limited to:
– Outdoor kitchens
– Window and door components
– Door skins
– Trim
– Façade cladding
– Fascia/soffit panels and other secondary exterior applications
– Wet interiors, including wall linings in swimming pools, bathrooms, changing rooms etc
– Signage
– Specialty furniture including lockers, cubicles, chairs & tables
– Play frames, tree houses & exterior composite furniture
– Sound barriers
Applications Brochures
About Tricoya
TRICOYA – A new breed of MDF
WHY TRICOYA?
Tricoya® creates a new class of MDF products with class 1 durability and exceptional dimensional stability, suitable for a wide range of exterior applications such as door skins and door panels, façade paneling, trim, fascia’s, soffits and many more uses.
Tricoya® can be cut, machined and installed using techniques and equipment commonly used throughout the building industry and requires low maintenance thereafter.
The flexibility of Tricoya® offers endless design opportunities so that it can be cut to size, machined CNC cut, painted, routed, wrapped without impacting its unique properties.
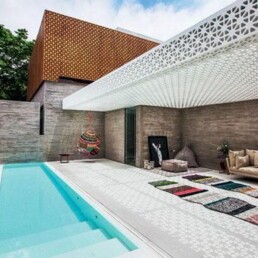
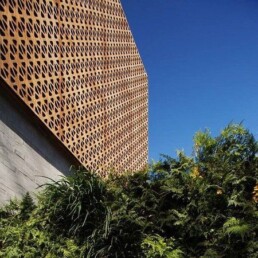
PERFORMANCE COMES NATURALLY
Many of the benefits observed in Accoya® solid acetylated wood, including enhanced dimensional stability, durability and fungal resistance, hold true for Tricoya®.
The functionality and versatility of wood-based composite panels give them universal appeal. Up until this point, the suitability of MDF panels for exterior and indoor constant wet use environments has been limited and over laid with practical limitations.
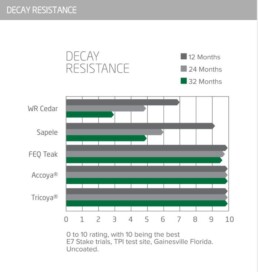
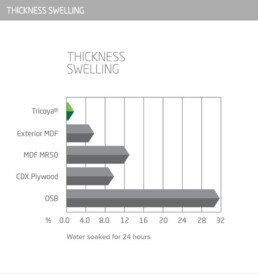
BENEFITS
Tricoya is characterised by its durability, dimensional stability and reliability properties. The new design and application possibilities offered by the marriage of acetylated wood fibre with the manufacturing technology of MDF is set to excite and stimulate composite product manufacturers, designers, architects and the construction industry alike, opening up new possibilities and solutions.
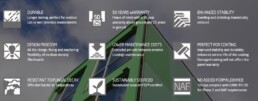